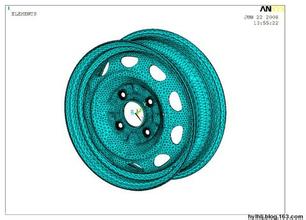
因摩托車輪的受力比較復雜,有限元分析在摩托車鋁合金車輪的設計中應用較少,尚未形成完善的分析體系這種情況對于新型摩托車及其車輪的設計推廣使用極為不利,如果進行有限元分析,必將大大縮短設計周期"降低設計成本,更快地將新型摩托車輪可靠地推向市場,并對老式摩托車輪的可靠性設計提供權威的理論依據。
有限元分析的過程通常是首先根據實驗建立正確簡化的力學模型,根據力學模型建立有限元分析模型進行分析,得出有限元分析結果,并對照材料的456曲線或物理性能,得出結論分析流程圖如圖所示。
(1) 在I-DEAS中meshing菜單下進行實體單元網格劃分。材料選擇A356,單元格長度為7 mm,進行網格劃分及網格質量檢查,直至檢查結果顯示為“0 elements storedas output group”,表明網格劃分成功,否則必須進行動態調整。
(2) 施加等效載荷在徑向彎曲疲勞分析中,載荷由兩部分組成:接觸應力、輪胎氣壓力。據實驗分析,摩托車在行駛過程中,車輪與地面接觸,受力范圍主要集中在80°區域,創建接觸應力:Q-徑向載荷N,Sr-系數,根據國家標準數值取2.25,W-車輪標定的最大設計載荷,1470N,故Traction=2.25×1470/8=413.4375N。創建輪胎氣壓力P:點選Pressure圖標,Use groupcurrent,輸入壓力大小為0.46 MPa。在“設置”圖標下選擇Combine,依次選擇F和Pressure。
(3) 點選“Manage Solve”圖標進行應力應變計算。在鋁車輪的滾動實驗中,一般采用云圖的方式進行后處理如圖所示。通過觀察儀可以發現,在徑向彎曲疲勞作用下,最先變形的是輪輞,顯示應力最大部位為輪輻與輪輞交接處。
(4) 疲勞分析應力計算完成之后,進行疲勞分析。在Durability下選擇Creat Event,并選中所施加的載荷。根據QC/T212-1996標準要求輸入壽命為5×e5r,進行計算。
從圖可以十分清楚地看到產品各不同部位的循環次數(壽命)和完成所有循環后的破壞系數,如圖所示最大破壞系數為7.74×e-2遠遠小于1,也就是綜合考慮可能會產生的實效因素,其破壞系數都小于1,因此不可能產生失效,所以對于該摩托車輪的徑向彎曲疲勞分析的結果是設計合理、壽命可靠。
專業從事機械產品設計│有限元分析│強度分析│結構優化│技術服務與解決方案
杭州納泰科技咨詢有限公司
本文出自杭州納泰科技咨詢有限公司m.yw15777.cn,轉載請注明出處和相關鏈接!