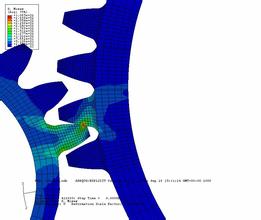
差減速機已廣泛的應用于化工、醫藥、食品、輕工、紡織、冶金、石油等各部門,充分顯示出了優越性。但是這種減速機在大功率小速比(i=6-17)范圍的使用過程中,常常因為同時接觸齒數少、面齒作用力大和齒面相對滑動速度大等原因而導致產生齒面膠合。為了解決齒面膠合問題,國內外先后研制開發了多齒差擺線針齒行星減速機。多齒差擺線針齒行星傳動由于避免了早期破壞和齒面膠合,并提高了整機的傳動扭矩,得到了較好的應用。但是,由于多齒差擺線針齒輪的形成原理,既多齒差擺線輪的齒廓是由多條不完整的齒廓曲線交叉構成,故齒頂為尖頂。使其齒廓頂部的強度不足為提高傳動性能,對尖頂需要進行必要的修正(簡稱修頂)。同時,因為齒面受力較為復雜,因此要對其齒面受力情況進行力學分析,同時對齒面強度也要進行分析。這里就是對多齒差擺線針輪進行強度分析和初步探討。
擺線針齒行星傳動一般為一齒差傳動(即針齒與擺線輪的齒數差為1),而實際上,只要在節圓上相差整數周節倍數就可實現多齒差傳動。多齒差擺線針齒行星傳動的齒形原理圖。它實際是由針齒和擺線輪相嚙合的一組傳動與由針齒和擺線輪相嚙合的另一組傳動組合而成的。擺線輪是由兩組齒廓構成,這兩組齒廓彼此干涉,最后留下不干涉部分而構成多齒差(二齒差)擺線輪的齒廓。因此該傳動的擺線輪齒數為12齒、針齒齒數為14齒。因此可知,一齒差擺線輪的齒廓為整枝曲線,而多齒差擺線輪的齒廓不是完整的曲線。值得注意的是,將一些差傳動改用多齒差傳動其速比并不改變。多齒差的傳動比i可用下式表示:i=輸入軸轉速/輸出軸轉速=Zz/Zz式中:Z-多齒差傳動擺線輪實際齒數;多齒差傳動針齒實際齒數。
從擺線針輪行星傳動的結構分析得知,該傳動可能的破壞形式主要有三種,一是擺線輪和針齒之間的膠合或點蝕破壞,應校核齒面的接觸強度。二是出現轉臂軸承的壽命不足現象,應校核其額定工作壽命。三是出現溫升過高,應進行熱平衡校該。而傳統結構形式中需要校核的針齒的彎曲強度、針齒的彎曲剛度、柱銷的彎曲強度等指標由于結構上的變化也只需要做一般驗證。無論做什么方面的驗證,擺線輪和針齒之間的接觸力,柱銷和柱鎖孔之間的接觸力計算都是必不可少的。理論齒形擺線輪和針齒分析如圖所示,設輸入扭矩為M,減速比為i,z,傳動效率為T,由于取消了針齒套和柱銷套增加了磨擦,所以傳動效率一般小于80%。設輸出扭矩M,則輸出扭矩M,(1)設擺線輪的理論齒數為Z,針輪的理論齒數為Z,擺線輪的實際齒數為Z,針輪的實際齒數為Zz。實際的擺線輪和針齒嚙合時,由于制造和安裝要求不可能滿足理論嚙合條件,必須對擺線輪進行合理的修形以便于裝拆和合理潤滑。修形后變小的擺線輪和針齒嚙合時,受力區域將會大大減少,精確的受力分析計算可參見文獻。受力區域參數可根據有關具體公式來驗算擺線輪和針齒齒面的接觸強度。
實踐表明,擺線輪和針齒面的失效形式是疲勞點蝕和膠和。齒輪嚙合齒面的應力、滑動速度、潤滑和零件制造精度,都是影響齒面產生疲勞點蝕和膠和的因素。為了防止產生點蝕和膠和的可能性,應進行擺線輪和針齒間的強度計算。齒面接觸應力應按下試計算可以看出:一齒差標準嚙合擺線針輪行星傳動減速器計算結果與相同參數的二齒差減速器相比較,按理論計算,齒面的最大接觸應力,二齒差是一齒差的95.9%,按實際計算,二齒差是一齒差的97%。一齒差標準嚙合擺線針輪行星傳動減速器計算結果與相同參數的三齒差減速器相比較,按理論計算,齒面最大接觸應力,三齒差是一齒差的88.9%,按實際計算,三齒差是一齒差的89.7%。說明多齒差結構可以有效地增加齒面的承載能力,將相對速度大的齒不參加傳力,從而也提高了整機的抗膠合能力,提高了強度。
專業從事機械產品設計│有限元分析│強度分析│結構優化│技術服務與解決方案
杭州納泰科技咨詢有限公司
本文出自杭州納泰科技咨詢有限公司m.yw15777.cn,轉載請注明出處和相關鏈接!